Blog
Comprehensive Analysis of Water Ring Vacuum Pumps
Table of Contents
Introduction to Water Ring Vacuum Pumps
Water ring vacuum pumps, commonly known as liquid ring vacuum pumps (LRVPs), are a distinct category of positive-displacement rotary machines. Their fundamental operation hinges on a rotating liquid, typically water, which acts as both a sealant and a working fluid. This liquid, propelled by centrifugal force, forms a dynamic “liquid ring” within a cylindrical casing, which then traps, compresses, and expels gases, thereby creating a vacuum. Centrifugal pumps, whose primary function is to increase the operating pressure of pumped fluids, LRVPs are specifically engineered to extract air or other gases from low-pressure vessels, establishing vacuum conditions below ambient atmospheric pressure.
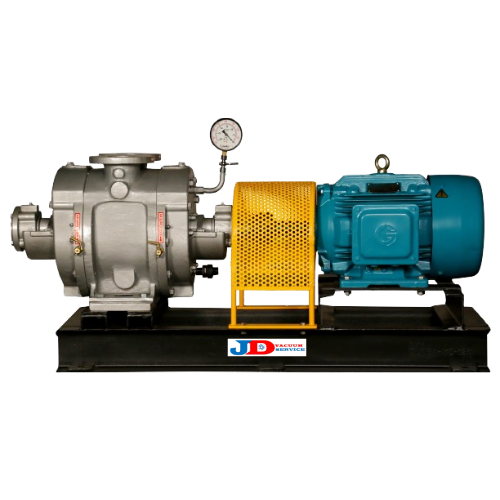
Beyond their primary role in vacuum generation, these pumps demonstrate remarkable versatility, being equally adept at functioning as gas compressors. This dual capability significantly broadens their utility across various industrial applications. The ability of a single device to perform two distinct yet related functions—creating a vacuum by removing gas and compressing gas—offers substantial operational flexibility. This can lead to optimized resource allocation and simplified system architecture, streamlining operations and potentially reducing capital expenditures for industries that require both functionalities.
The robust design and operational flexibility of LRVPs render them indispensable across a wide spectrum of industrial sectors. They serve as critical components in the chemical, petrochemical, pharmaceutical, food processing, pulp and paper, mining, and energy production industries. A particular strength of these pumps lies in their capacity to manage challenging process media, including highly explosive gases, moist or humid gas streams, corrosive vapors, and gases laden with particulates. This inherent tolerance allows LRVPs to operate reliably and safely in harsh industrial environments where other vacuum technologies might fail or necessitate extensive pre-treatment. This characteristic establishes a unique market niche for LRVPs. While other vacuum pump types, such as rotary vane or dry screw pumps, may offer higher efficiency or deeper vacuum for clean applications, their sensitivity to contaminants severely limits their use in demanding environments. The LRVP’s intrinsic capability to dilute or wash through these substances with its sealing liquid provides a significant competitive advantage for rugged, real-world applications, justifying their continued widespread adoption despite potentially lower stated efficiency.
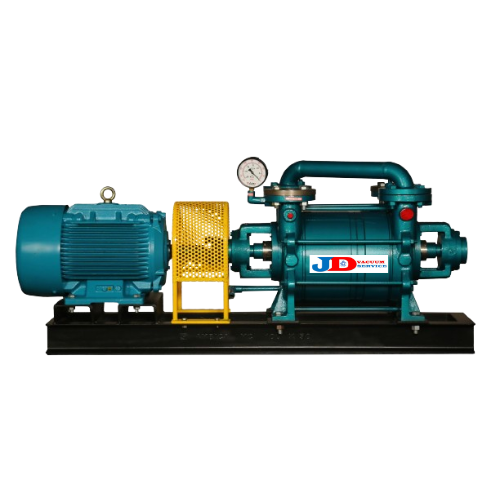
Fundamental Principles and Mechanics of Operation
The operational foundation of water ring vacuum pumps is rooted in a simple yet effective principle. An impeller is positioned eccentrically within a cylindrical casing, which is partially filled with a sealing liquid, typically water.
The Liquid Ring Principle Explained
As the impeller rotates, centrifugal force acts upon the liquid, compelling it outwards to form a dynamic, concentric “liquid ring” against the inner wall of the cylindrical casing. This rotating liquid ring effectively creates a series of sealed chambers within the spaces defined by the impeller vanes, which are essential for the subsequent gas compression process.
Centrifugal Force and Vacuum Creation
The eccentric mounting of the impeller relative to the cylindrical housing means that while the liquid ring is concentric with the housing, it remains eccentric to the impeller itself. This eccentricity causes the volume of the individual chambers, or cells, formed between the impeller vanes and the liquid ring, to continuously expand and contract during each full rotation. As these cells enlarge while passing the pump’s inlet port, they draw in air or other process gases from the suction pipe. This action effectively creates the desired vacuum, functioning in a manner analogous to the suction stroke of a piston in a cylinder. This analogy is crucial for understanding the positive displacement nature of LRVPs, indicating that they trap a fixed volume of gas and move it, leading to predictable flow characteristics compared to dynamic pumps.
Gas Compression and Discharge Cycle
Following the suction phase, as the impeller continues its rotation, the liquid ring converges towards the impeller hub. This convergence progressively reduces the volume of the trapped gas within each cell. This reduction in volume results in the compression of the gases. Once compressed, these gases, along with a portion of the sealing liquid, are expelled through the pump’s discharge port. The entire operational sequence—suction, compression, discharge, and subsequent expansion—occurs in a continuous, cyclical manner, ensuring a steady vacuum or compression flow.
A significant operational benefit of this liquid-based mechanism is the inherent ability of the liquid seal to cool and condense the gases being conveyed. This continuous cooling and condensing action is a built-in advantage. The isothermal compression means that the temperature rise during gas compression is minimal because the liquid continuously absorbs heat from the gas. This direct relationship implies that LRVPs are uniquely suited for handling flammable and explosive gases and condensable vapors. The risk of ignition from temperature spikes is significantly reduced, and vapors are condensed, which enhances vacuum efficiency by reducing the volume of gas that needs to be evacuated. This makes them a safer and more effective choice in industries like chemical and pharmaceutical manufacturing where such gas characteristics are prevalent.
Key Components and Construction Details
The effective operation of a water ring vacuum pump relies on the precise interaction of several key components, each constructed from materials selected for durability and application suitability.
Primary Components
- Cylindrical Housing (Casing): This robust outer shell encloses the impeller and contains the crucial sealing liquid. Its construction is vital for maintaining the vacuum and facilitating the formation of the liquid ring.
- Impeller (Rotor): As the sole moving part within the pump, the impeller features a series of blades or vanes. Its eccentric positioning within the cylindrical casing is fundamental to creating the expanding and contracting chambers necessary for gas handling.
- Sealing Liquid (Operating/Service Liquid): Typically water, but also potentially oil or a methanol-water mixture, this fluid is introduced into the housing to form the essential liquid ring. It functions as both a dynamic piston for gas compression and a hermetic seal. A minimum volume, often around one-quarter of the cylinder, must be filled before pump operation commences.
- Inlet (Suction) Port/Pipe: This is the entry point for air or process gases, initiating the vacuum creation cycle.
- Discharge Port/Pipe: This is the exit point for compressed gases and a portion of the sealing liquid, completing the compression cycle.
- Shaft Seals: These critical components prevent sliding friction and ensure the integrity of the vacuum by preventing leakage along the rotating shaft.
- Bearings: Supporting the rotating shaft, bearings are essential for smooth operation and require consistent lubrication to minimize friction and wear.
- Liquid Separator: Often integrated downstream of the pump, this vessel efficiently separates the operating fluid from the discharged gas. This separation is vital for allowing the reuse of the liquid and preventing its dilution, particularly in recirculation systems.
- Heat Exchanger: Especially relevant in recirculation systems, a heat exchanger cools the sealing liquid. This process effectively manages and dissipates the heat generated during pump operation, maintaining optimal liquid temperature and pump efficiency.
Materials of Construction
Manufacturers prioritize durability, utilizing robust materials such as cast iron for general industrial applications and stainless steel for more demanding environments. For highly corrosive conditions, special alloys or protective coatings are applied; for instance, the pharmaceutical and food industries frequently specify stainless steel to ensure hygiene and superior corrosion resistance. Impellers are commonly fabricated from high-quality stainless steel or bronze to withstand operational stresses and resist corrosion. Shafts are typically constructed from alloy steel, often with surface treatments to enhance strength and wear resistance, crucial for long-term reliability. Seals are made from high-grade elastomers, chosen for their sealing effectiveness and resistance to the pumped media. In some designs, the housing may be made from cast aluminum with specialized protective coatings for specific applications. The ultimate choice of construction materials is critically dependent on the specific chemical and physical properties of the liquid and gas being handled, ensuring optimal performance and longevity. This highlights that material selection is a critical design decision driven by application severity. The specific process conditions, such as the presence of corrosive chemicals, hygienic requirements, or abrasive particles, directly dictate the optimal material choice. This choice, in turn, significantly influences the pump’s durability, its resistance to wear and corrosion, and ultimately its operational lifespan and the frequency and cost of maintenance. A suboptimal material choice will inevitably lead to premature failure, increased downtime, and higher operational expenditure. This emphasizes that pump selection is not merely about achieving a certain vacuum capacity but involves a holistic engineering decision that thoroughly considers the chemical and physical properties of the media to ensure long-term reliability and cost-effectiveness.
Design Variations: Cone Type vs. Flat Plate Type
Liquid ring vacuum pumps are primarily available in two internal design configurations:
- Cone Type: In this design, the impeller blades are precisely machined to rotate around a conical surface, maintaining a close, non-contact fit. The overall effectiveness of the pump is highly dependent on the efficiency of the sealing action between the rotor blades and this cone. A significant advantage of cone-type designs is their large ports, which facilitate the easy passage of process liquids and entrained solids. Furthermore, they possess the ability to re-establish clearances, thereby helping to regain original performance over time. This implies that the cone-type design, despite potential manufacturing complexity, offers superior operational resilience, particularly in contaminated environments. The ability to handle “slugs of process water and entrained solids” and “re-establish clearances” suggests a self-cleaning or self-correcting mechanism inherent in the cone design, making it inherently more resilient to the very contaminants that LRVPs are often chosen to handle. This indicates that for demanding, dirty applications, the cone type, despite potentially higher initial cost, often offers a lower total cost of ownership due to significantly reduced downtime, extended service intervals, and maintained performance over time.
- Flat Plate Type: This design employs a port plate configuration instead of a cone. While the fundamental working principle remains consistent with the cone type, flat plate designs are generally simpler and easier to manufacture. However, they are typically less efficient than their cone-type counterparts.
Multi-stage Configurations
Multi-stage pumps, particularly two-stage designs, are engineered to achieve deeper vacuum levels. They typically consist of two single-stage pumps connected in series on a common shaft. In this configuration, the first stage initiates the vacuum by generating a preliminary pressure reduction, while the second stage further compresses the gas, enabling the pump to reach significantly deeper vacuum levels. The unique offset design of the body casing from the rotor axis in multi-stage pumps, with the second stage offset diametrically opposite the first, is engineered to balance forces on the rotor. This meticulous design ensures remarkably smooth and quiet operation, enhancing the pump’s reliability and suitability for sensitive environments.
The separation and cooling of sealing liquid are crucial system-level considerations, not just isolated pump components. Liquid separators and heat exchangers are integral parts of the overall system. This indicates that the LRVP is rarely a standalone unit in industrial settings; it functions as part of a larger, interconnected system. The purpose of these auxiliary components, such as saving operating fluid, preventing dilution, and cooling the liquid, directly impacts the pump’s efficiency, water consumption, and environmental discharge. For instance, a full recovery system with a heat exchanger can reduce water consumption to near zero, directly addressing a key disadvantage of LRVPs (high water requirement ). This implies that optimizing LRVP operation extends beyond the pump itself to the design and meticulous management of its auxiliary systems. This holistic approach influences both economic factors, such as water cost and energy for cooling, and critical environmental considerations, such as effluent treatment and discharge regulations, making system design as important as pump selection.
Types and Design Variations of Water Ring Vacuum Pumps
Water ring vacuum pumps are available in various configurations, each tailored to specific operational requirements and performance envelopes. These variations include the number of stages, the action of the impeller, and the overall system design for managing the sealing liquid.
Single-Stage vs. Two-Stage Pumps
The choice between single-stage and two-stage pumps represents a fundamental trade-off between cost, simplicity, vacuum depth, and efficiency, directly impacting application suitability.
Single-Stage Pumps:
- Definition: These pumps are characterized by a single impeller configuration, which creates a vacuum by drawing in and expelling gas only once per impeller revolution.
- Characteristics: While capable of delivering higher vacuum levels in certain single-acting designs, they generally exhibit lower pumping speed and efficiency compared to their double-acting or two-stage counterparts.
- Performance: Single-stage pumps typically achieve moderate vacuum levels, ranging up to 26-29 inches of mercury (inHg) or approximately 33 mbar (absolute). Their efficiency tends to decrease at higher vacuum levels, making them best suited for applications where deep vacuum is not the primary requirement.
- Applications: They are commonly employed for basic HVAC tasks, packaging, food processing, and in laboratory settings where moderate vacuum levels suffice and critical deep vacuums are not essential.
- Advantages: Offer a lower initial investment and generally incur lower operational costs. Their simpler design translates to easier maintenance and provides adequate performance for many standard industrial applications.
Two-Stage Pumps:
- Definition: These advanced configurations incorporate two impellers arranged in series, typically on a common shaft. The first stage initiates the vacuum, and the second stage further reduces the pressure, enabling the achievement of significantly deeper vacuums.
- Characteristics: Two-stage pumps are designed to maintain high pumping speeds even when operating at higher vacuum levels, ensuring stable and consistent performance.
- Performance: They can achieve substantially deeper vacuum levels, often exceeding 29 inches of mercury (inHg) or reaching as low as 0.5 mbar (absolute). They demonstrate improved efficiency at higher vacuum levels (above 23 inHg), making them ideal for demanding processes.
- Applications: Preferred in high-precision industries such as pharmaceuticals, electronics manufacturing, and chemical processing. They are highly effective for applications involving solvents or volatile substances that necessitate extremely low-pressure environments. Additionally, they are known for providing quick evacuation times and contributing to cleaner operations.
- Advantages: Provide superior efficiency in achieving deeper vacuums and are better suited for handling gases that may condense or react under lower pressures. Their enhanced performance makes them particularly beneficial in demanding industrial environments.
- Disadvantages: Generally entail higher initial purchase costs and potentially higher maintenance expenses due to their increased complexity and additional components.
The following table provides a concise comparison of single-stage and two-stage water ring vacuum pumps:
Characteristic | Single-Stage Water Ring Vacuum Pump | Two-Stage Water Ring Vacuum Pump |
---|---|---|
Number of Impellers | 1 | 2 (arranged in series) |
Vacuum Level Achievable | Moderate (up to 26-29 inHg / ~33 mbar abs) | Deeper (exceeding 29 inHg / ~0.5 mbar abs) |
Efficiency at High Vacuum | Lower | Higher (especially above 23 inHg) |
Cost (Initial/Maintenance) | Lower | Higher |
Complexity | Simpler | More Complex |
Typical Applications | Packaging, Food Processing, HVAC, Basic Laboratories | Pharmaceuticals, Electronics Manufacturing, Chemical Processing, Solvents |
This comparison highlights that selecting the appropriate pump is not about identifying an inherently “best” pump, but rather the most suitable one for the specific vacuum requirements and budget constraints of a given application. Over-specifying, such as deploying a two-stage pump for a moderate vacuum application, leads to unnecessary capital expenditure and higher operational costs. Conversely, under-specifying, like using a single-stage pump for a deep vacuum requirement, results in inadequate performance and potential process inefficiencies. This underscores the critical importance of a precise and thorough vacuum requirements assessment during the initial design phase of any industrial system.
Single-Acting vs. Double-Acting Pumps
- Single-Acting: In this design, suction and exhaust occur only once during each complete revolution of the impeller.
- Double-Acting: These pumps are engineered to perform both suction and exhaust twice per impeller revolution. This design significantly reduces the overall size and weight of the pump for a given pumping speed. The symmetrical distribution of the working chamber on both sides of the impeller also improves load distribution on the rotor, leading to higher pumping speeds and enhanced efficiency, though with slightly lower ultimate vacuum levels compared to single-acting designs.
Atmospheric Liquid Ring Pumps
This specialized configuration combines a standard liquid ring pump with an atmospheric ejector. The atmospheric ejector, positioned in front of the liquid ring pump, serves to enhance the achievable vacuum levels. This synergistic arrangement effectively expands the pump’s operational range, allowing it to reach deeper vacuums than a standalone liquid ring pump.
System Configurations (Fluid Systems)
The management of the sealing liquid within water ring vacuum pump systems has evolved into three primary configurations, each with distinct advantages and disadvantages, reflecting a progression driven by environmental concerns and operational cost optimization.
- Once-Through System: In this basic configuration, the sealing liquid is fed into the pump system only once. After performing its function, the discharged fluid, a mixture of gas and liquid, is directed to a separator vessel where the gas is vented, and the liquid is then drained as waste. This system is straightforward to operate as it involves no recirculation or recovery of the sealing liquid. While it has no high initial capital costs for auxiliary recirculation equipment , it suffers from high water consumption and associated disposal costs, especially if the water becomes contaminated and requires cleaning prior to discharge. This system also necessitates an effluent treatment setup, adding to operational expenses and environmental considerations.
- Partial Recirculation System: This system builds upon the once-through design by incorporating a separator tank where a portion of the sealing liquid is recirculated back to the pump. To maintain the liquid level and temperature, makeup water is continuously added. An equivalent amount of discharged liquid is simultaneously drained as waste. The introduction of fresh sealing liquid helps to maintain the proper operating temperature, which is crucial for minimizing the risk of cavitation and facilitating better pump maintenance. This configuration avoids the high initial costs associated with full recovery systems and consumes less sealing liquid compared to once-through systems due to partial recirculation. However, it still requires a continuous supply of makeup water for cooling and replenishment, which can incur ongoing water costs.
- Total Recirculation System (Full Recovery): This represents the most advanced and environmentally conscious configuration, where the sealing fluid is contained within a closed-loop system and continuously recycled. A heat exchanger is integral to this system, removing the heat generated during compression and cooling the sealing fluid before it is reintroduced into the pump. Proper management of the seal liquid level in the separator, typically slightly below the pump shaft centerline, and high-level overflow provisions are necessary to prevent pump motor damage and overloading during startup. In systems with significant pressure drop, a circulation pump may be required. This system is ideal for high vapor services and offers significantly reduced or even zero sealing liquid discharge, making it highly environmentally friendly. It is particularly suitable for facilities where water availability is limited or discharge regulations are stringent, such as landlocked dairies. The progression from once-through to partial and then to total recirculation systems is not an arbitrary development. The explicit drawbacks of the once-through system, such as high water cost, disposal cost, and the requirement for effluent treatment , directly led to the development and adoption of recirculation systems. This establishes a clear cause-and-effect relationship: increasing water costs and increasingly stringent environmental regulations, particularly regarding effluent discharge, serve as powerful drivers for innovation towards more closed-loop systems. The total recirculation system, with its potential for zero discharge , represents the ultimate response to these pressures, even if it involves higher initial and maintenance costs. This implies a broader industry trend towards sustainability and resource efficiency, where the initial capital expenditure for more complex, environmentally friendly systems is justified by significant long-term operational savings and the imperative of regulatory compliance.
Operational Characteristics and Performance Parameters
Understanding the operational characteristics and key performance parameters of water ring vacuum pumps is crucial for their effective selection, deployment, and optimization in industrial settings.
Ultimate Vacuum Levels
The ultimate vacuum level achievable by a water ring vacuum pump is a critical performance indicator. Single-stage pumps typically achieve moderate vacuum levels, generally up to 26-29 inches of mercury (inHg) , which corresponds to approximately 33 mbar (absolute). In contrast, two-stage pumps are designed for deeper vacuum applications, capable of exceeding 29 inHg and reaching as low as 0.5 mbar (absolute). The achievable vacuum is fundamentally limited by the saturated vapor pressure of the working liquid, meaning that with water as the working liquid, the ultimate pressure can only reach 2000-4000 Pa (20-40 mbar), while using oil as the working fluid can achieve lower pressures, down to 130 Pa (1.3 mbar).
Flow Rate Ranges and Capacities
The volume capacity, or flow rate, of LRVPs varies significantly based on their size and design. Smaller pumps may handle a few cubic meters per hour, whereas larger industrial units can manage several thousand cubic meters per hour. For instance, some industrial two-stage pumps can handle capacities up to 800 m³/h , while high-capacity models can range from 700 m³/h to 23,000 m³/h. This wide range allows for application in diverse processes, from small-scale laboratory work to large-scale industrial operations.
Efficiency Metrics
The efficiency of liquid ring vacuum pumps is typically assessed through two primary metrics:
- Isothermal Efficiency: This metric reflects how effectively a pump compresses gas without a significant temperature rise. It is a direct consequence of the liquid ring’s ability to absorb heat during compression.
- Overall Efficiency: This combines volumetric and isothermal efficiencies, indicating how well the pump converts input power into useful work. Typically, liquid ring vacuum pumps exhibit overall efficiencies ranging from 30% to 50%, depending on operational conditions and design factors. While this efficiency may be lower compared to other vacuum pump technologies like rotary vane (60-90%) or screw pumps (50-80%), LRVPs are often preferred in applications involving condensable vapors due to their ability to handle such gases effectively without significant energy losses.
Factors Influencing Performance
Several critical factors significantly impact the performance and efficiency of water ring vacuum pumps:
- Working Fluid Temperature: The temperature of the sealing liquid directly affects its vapor pressure and the pump’s energy efficiency. Higher temperatures can lead to increased vaporization within the pump, reducing the achievable vacuum and overall efficiency. Maintaining optimal working fluid temperatures is crucial for performance.
- Atmospheric Pressure: The ambient atmospheric pressure at both the inlet and outlet of the pump has a notable influence on performance. Pumps are typically designed and rated under standard atmospheric pressure conditions, and deviations due to altitude or weather can alter performance.
- Speed of Rotation (RPM): The rotational speed of the impeller affects shaft power, mechanical loss rates, and hydraulic loss power. While increasing speed can increase shaft power, it may also decrease efficiency due to increased losses, potentially leading to uneconomical operation or even hazardous conditions if not properly managed.
- Gas Composition and Temperature: The specific composition and temperature of the gases being pumped are vital design parameters. Deviations from original design conditions can lead to performance problems.
- Humidity: High humidity in the gas stream can be tolerated by LRVPs, but it can also influence the working fluid’s properties and overall pump performance.
- Air Leakage: Excessive air leakage into the system can significantly reduce the pump’s suction capacity and overall vacuum performance. Regular checks, such as drop tests, are essential to identify and rectify leaks.
- Inlet Design and Restriction: The design of the inlet port influences flow dynamics and efficiency. Any restriction or clogging in the inlet pipe can severely decrease suction capacity.
- Back Pressure: Confirming that the back pressure aligns with design conditions is important, as excessive back pressure can lead to persistent overheating and reduced performance.
- Quality of Make-up Water: The quality of the water used for the liquid ring, including impurities and viscosity, can affect pump performance and lead to issues like scaling or corrosion.
- Nozzle Condition: In certain pump designs, the condition of nozzles (if present) is critical. Issues like wrong installation, skew, blockage, damage, corrosion, or leakage can significantly impair performance.
Industry Standards and Compliance
To ensure reliability and consistent performance, water ring vacuum pumps are often designed and tested in compliance with global and industry standards. A notable example is the Hydraulic Institute (HEI) Test Process, which provides industry standards and factory test methods for liquid ring vacuum pumps and compressors. These standards include definitions, nomenclature, design specifications, operating variables, and correction factors, ensuring that pumps meet established performance benchmarks. Compliance with these standards provides assurance of the pump’s quality and operational integrity, particularly for critical applications like maintaining vacuum in steam condensers in power plants.
Advantages and Disadvantages
Water ring vacuum pumps possess a unique set of characteristics that make them highly suitable for specific industrial applications, while also presenting certain limitations that must be considered during selection and operation.
Benefits
- Ability to Handle Wet, Humid, or Condensable Gases: One of the most significant advantages of LRVPs is their exceptional tolerance for wet, humid, or vapor-laden gases without sustaining damage. The liquid ring acts as a natural seal, allowing them to manage liquid carryover more effectively than many other vacuum pump types. This makes them ideal for processes involving condensation, evaporation, and degassing.
- High Tolerance for Contaminants: These pumps are remarkably robust in environments with dirty or unrefined gases. Particulates, impurities, and caustic substances are diluted and discharged along with the fluid, making them highly suitable for harsh conditions, such as those with extreme humidity or in industries like wastewater treatment, pulp and paper manufacturing, and mining operations where contaminant-laden gases are common.
- Simple and Robust Design: The straightforward design of LRVPs, typically involving only one primary moving part (the impeller), contributes to high reliability, minimal wear, and reduced maintenance requirements. This simplicity also means they are less prone to breakdowns or malfunctions.
- Quiet Operation and Low Vibration: Water ring vacuum pumps are known for their quiet operation and low vibration levels. The movement of water prevents the propagation of vibrations, making them suitable for noise-sensitive environments and enhancing workplace comfort.
- Isothermal Compression: The compression process within LRVPs is nearly isothermal, meaning the temperature of the compressed gas changes very little. This characteristic is due to the continuous heat dissipation by the sealing liquid, which reduces the risk of unwanted explosions and makes them suitable for handling flammable and explosive gases.
- Built-in Cooling: The sealing liquid inherently absorbs heat generated during compression, preventing overheating and boosting efficiency. This internal cooling mechanism is a distinct advantage.
- Chemical Compatibility: The materials of construction can be customized to resist corrosion, allowing these pumps to safely handle aggressive chemicals.
- Versatility: LRVPs can function as both vacuum pumps and compressors, making them adaptable to a wide range of applications and processes. They can also operate at varying vacuum levels and flow rates, offering significant flexibility.
Limitations
- Dependence on Sealing Liquid: A primary drawback is their reliance on a continuous supply of sealing liquid, typically water. This requirement increases operational costs and necessitates proper water treatment to prevent issues like scaling or corrosion within the pump.
- Energy Efficiency: Water ring vacuum pumps tend to be less energy-efficient compared to dry vacuum pumps, especially when operating at deeper vacuum levels. Their efficiency generally ranges from 30% to 50%.
- Size and Weight: Their physical size and weight can be relatively large, which may limit installation flexibility in space-constrained environments.
- Contamination Risks: If not properly managed, the liquid used for sealing can introduce contamination risks, particularly in hygienic or sterile processes.
- Unsuitable for Dry, Dust-Laden Gases (without specific provisions): While they tolerate some particulates, these pumps are generally not ideal for handling purely dry, dust-laden gases, as solid particles can damage internal components and reduce the pump’s lifespan if not diluted or separated effectively.
- Limited Vacuum Degree with Water: When water is used as the working fluid, the ultimate vacuum degree is limited by its saturated vapor pressure, typically reaching only 2000-4000 Pa.
Industrial Applications
Water ring vacuum pumps are crucial components across a diverse array of industries, owing to their unique design and operational capabilities that enable efficient gas removal, solvent recovery, and moisture extraction. Their robustness and ability to handle challenging media make them highly versatile.
Detailed Applications Across Various Sectors
- Chemical and Pharmaceutical Industry: LRVPs are extensively used as both compressors and vacuum pumps in these sectors. Specific processes include distillation, solvent recovery, filtration, drying, degassing, molecular distillation, filling, cooling, crystallizing, and deaeration of caustic solutions. Their chemical compatibility ensures safe operation with corrosive and volatile substances.
- Pulp and Paper Industry: These pumps are vital for dewatering paper webs and paper coating processes, where their tolerance for moisture and contaminants is highly beneficial.
- Food Industry: Applications include bottling, sausage production, sweet production, degasification of mineral water, and powder conveying. Their suitability for non-toxic fluids like water makes them ideal for hygienic environments.
- Energy Production (Power Plants): LRVPs are used to maintain low pressure in steam condensers, extract non-condensable gases from turbines to increase efficiency, and for waterbox priming applications. They also assist in dewatering gypsum, a byproduct of Flue Gas Desulphurisation systems, on vacuum filters.
- Mining Industry: Key applications include vacuum filtration, gas boosting, and drawing off pit gas.
- Automobile Industry: Utilized for engine testing, carburetor testing, and vacuum filling of power steering and brake fluid.
- Petroleum Industry: Employed for vacuum priming, vacuum cleaning and filling of barrels, filtration, and vapor recovery.
- Plastic Industry: Applications include extrusion degasification, vacuum calibration, and drawing off and compressing vinyl chloride gas.
- Textile Industry: Primarily used for hydro extractor applications.
- Environmental Engineering: They assist in soil remediation and wastewater treatment, leveraging their ability to handle contaminant-laden gases.
- Aeronautical and Mineral Processing: LRVPs also find use in these and other industrial applications.
Specific Processes Benefiting from LRVPs
- Distillation: By creating a vacuum, LRVPs lower boiling points, facilitating the separation of components based on volatility, enhancing efficiency and product purity in distillation columns.
- Solvent Recovery: They are crucial for recovering volatile solvents from waste streams, reducing environmental impact and operational costs. Their ability to operate under varying conditions makes them ideal.
- Filtration: LRVPs generate a vacuum to facilitate faster and more efficient removal of unwanted solids or liquids from mixtures, ensuring high product quality and reducing processing time.
- Drying: The vacuum environment created by LRVPs accelerates evaporation rates, effectively removing moisture or solvents from products, leading to shorter drying times and improved product consistency.
- Degassing: They efficiently remove dissolved gases from liquids or slurries by creating a vacuum that allows gases to escape without introducing contaminants.
- Molecular Distillation: For specialized applications, LRVPs provide the necessary low-pressure environment to separate compounds based on their molecular weight, useful in refining high-value chemicals and pharmaceuticals.
- Pneumatic Conveying: Within chemical plants, LRVPs help transport powders and granules through pipelines by creating the required vacuum pressure.
Maintenance Requirements and Troubleshooting
Effective maintenance is paramount to ensuring the optimal performance, longevity, and reliability of water ring vacuum pumps. Neglecting maintenance can lead to common operational problems and costly downtime.
Essential Maintenance Procedures
- Inspect and Change Sealing Liquid: The sealing liquid is crucial for pump operation. Its level and quality must be regularly checked, ensuring it is clean and free from contaminants. Periodic changing of the sealing liquid, according to manufacturer guidelines, is often necessary.
- Check for Leaks: Vacuum pump efficiency heavily relies on tight seals. Regular inspection of the pump and its connections for any signs of leakage (e.g., hissing sounds, visible leaks, pressure drop) is vital. Leaks negatively impact performance and require prompt attention.
- Inspect and Clean Inlet Filters: Inlet filters prevent debris and contaminants from entering and potentially damaging the pump. These filters should be regularly inspected and cleaned to prevent clogging and replaced as needed following manufacturer recommendations.
- Monitor Temperature and Cooling: Water ring vacuum pumps generate heat during operation. It is essential to monitor their temperature and ensure the cooling system functions correctly. Overheating can lead to pump failure or reduced efficiency, so temperature gauges should be watched, and any issues addressed promptly.
- Lubrication: Many components, such as bearings and shaft seals, require lubrication. Following the manufacturer’s guidelines for the type and frequency of lubrication can significantly extend the pump’s lifespan and reduce wear and tear. Both over-lubrication and under-lubrication can be detrimental.
- Regular Vibration Analysis: Conducting regular vibration analysis helps detect anomalies in the pump’s operation. Increased vibration can indicate issues such as misalignment, worn bearings, or other problems requiring immediate attention to prevent costly repairs or pump failure.
- Inspect and Maintain the Motor: The motor driving the pump is a critical component that needs regular inspection for signs of overheating, unusual noise, or vibration. It should be kept clean and well-lubricated, with any necessary maintenance or repairs performed according to manufacturer recommendations.
- Perform Routine Performance Checks: Regularly monitoring the pump’s performance, including its suction capacity and pressure levels, is important. Any significant deviations from the pump’s normal operating parameters should be investigated to identify and address potential issues.
- Scheduled Overhauls: Depending on operating conditions and manufacturer recommendations, scheduled overhauls should be planned. During an overhaul, the pump is disassembled, and components are inspected, repaired, or replaced as necessary to maintain performance and extend lifespan.
- Keep Records: Maintaining detailed records of all maintenance activities, inspections, and repairs is valuable for tracking the pump’s history, identifying recurring issues, and ensuring timely maintenance.
- Training and Education: Personnel responsible for maintenance should be adequately trained and educated about the equipment to help them identify problems early and perform tasks correctly.
- Consult the Manufacturer: Always refer to the manufacturer’s specific maintenance guidelines and recommendations for your water ring vacuum pump model, as they provide valuable insights into best practices.
Common Operational Problems
Liquid ring vacuum pumps can experience several general operational problems:
- Stalling during operation, starting failure, or low/poor pumping capacity: These are common issues that often point to underlying maintenance needs.
- Cavitation: This critical problem involves the development of small, crater-like holes on the impellers, leading to poor performance and a reduced lifespan for the machine. It typically occurs when the service liquid cannot maintain the vacuum level without boiling or vaporization.
- Excessive Horsepower Consumption: This can be caused by belt misalignment or poor tensioning, water overload, inlet restriction, motor problems, or pump over-speeding.
- Leakages: Water leakages primarily occur due to damaged seals, gland packing, body gaskets, or body plugs.
- Unusual Noises or Vibrations: These can indicate issues such as flooding, misalignment of belts or couplings, pump mounting problems, faulty bearings, or excessive wear.
- Persistent Overheating: This can be caused by high inlet temperatures, a high compression quotient, a faulty cooling system, or clogging of the discharge port, which increases back pressure.
Troubleshooting Guide for Key Issues
Reduced Pump Performance:
- Inspect suction and discharge lines for leaks or blockages.
- Check impellers for signs of wear or damage and replace if necessary.
- Ensure the seal liquid flow rate is within the recommended range.
- Monitor the seal liquid used and its vapor pressure, as changes can affect vacuum levels.
- Analyze original design parameters against current operating conditions, especially regarding gaseous composition and cooling water temperature.
- Confirm back pressure is as per design conditions.
Unusual Noises or Vibrations:
- Inspect the pump for signs of misalignment (belts or couplings) and adjust if necessary.
- Check bearings for signs of wear or damage and replace if needed.
- Look for signs of cavitation, such as pitting or erosion on the impellers, and address the issue promptly.
- Ensure proper pump mounting.
Overheating:
- Monitor the cooling water flow rate and adjust as necessary.
- Regularly clean heat exchangers to remove any debris or contaminants.
- Ensure proper lubrication of the pump’s bearings and other moving parts.
- Check for high inlet temperatures or clogging of the discharge port.